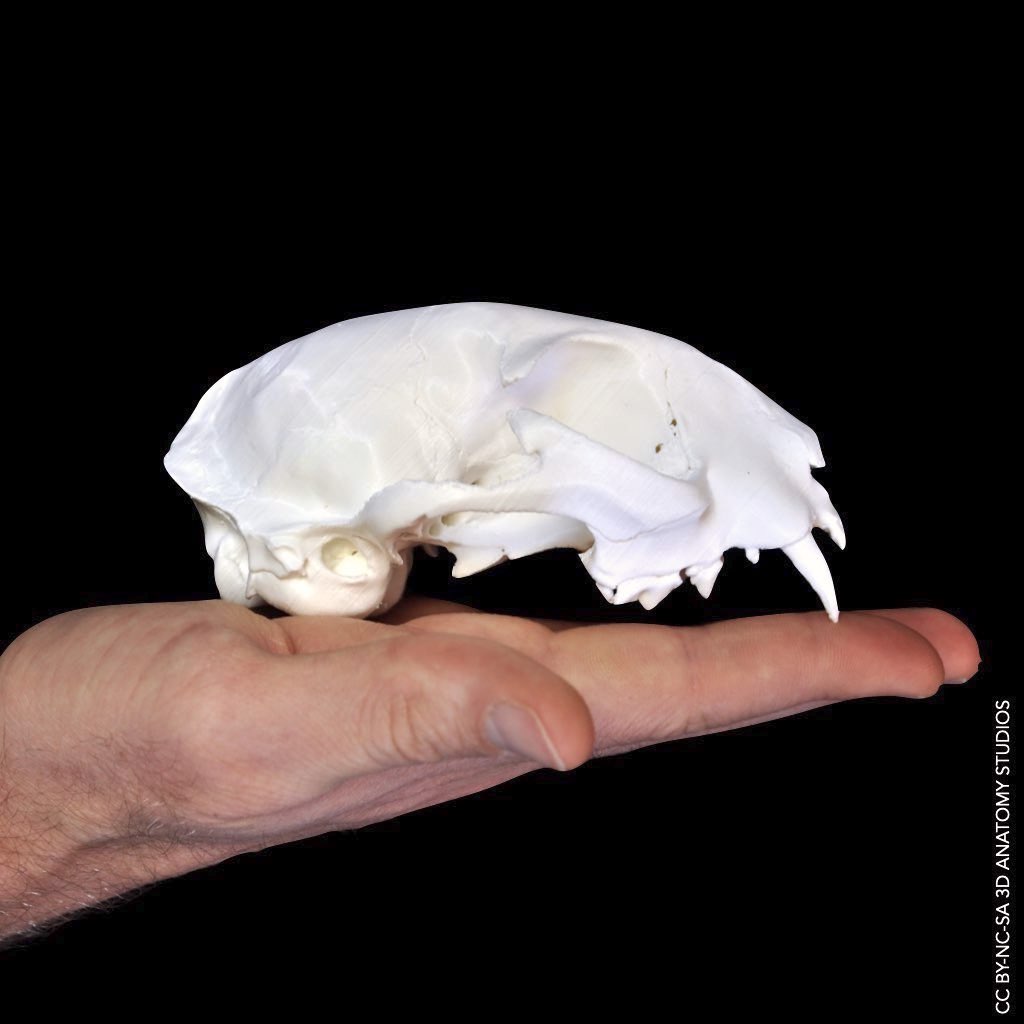
If you’ve ever tried buying clothes online, you’ve experienced the great challenge of understanding a physical object through a virtual interface and photographs. Yes, you can get a basic grasp of the color and pattern or design but the feel of the fabric, the fit on your body, the look from the front versus the side or back, how it conforms to your movements; these fundamental properties of clothes are impossible to understand virtually. Yet, once you have that item of clothing physically in hand, you would see and feel these properties the instant you try it on. That is the power of learning through physical interaction.
What is true for clothing is even more true for learning or researching anatomy, where there are parts with unfamiliar and complex geometries, lengthy lists of terms, and numerous interactions among parts. Unlike virtual models, which engage only your visual sense, you can handle and manipulate physical anatomical models to engage your visual and tactile senses simultaneously; not only do you learn better with “multisensory” (vs. unisensory) learning, you’re more likely to remember what you learn (Shams & Seitz, 2008; Ekwueme et al., 2015). It’s also easier to test physical interactions with physical models, such as how two bones articulate, how fluid flows across or around a structure, or the consequence of different moment arms for leverage. And orientation and scaling become more intuitive once you can orient a physical model relative to other models or your own body.
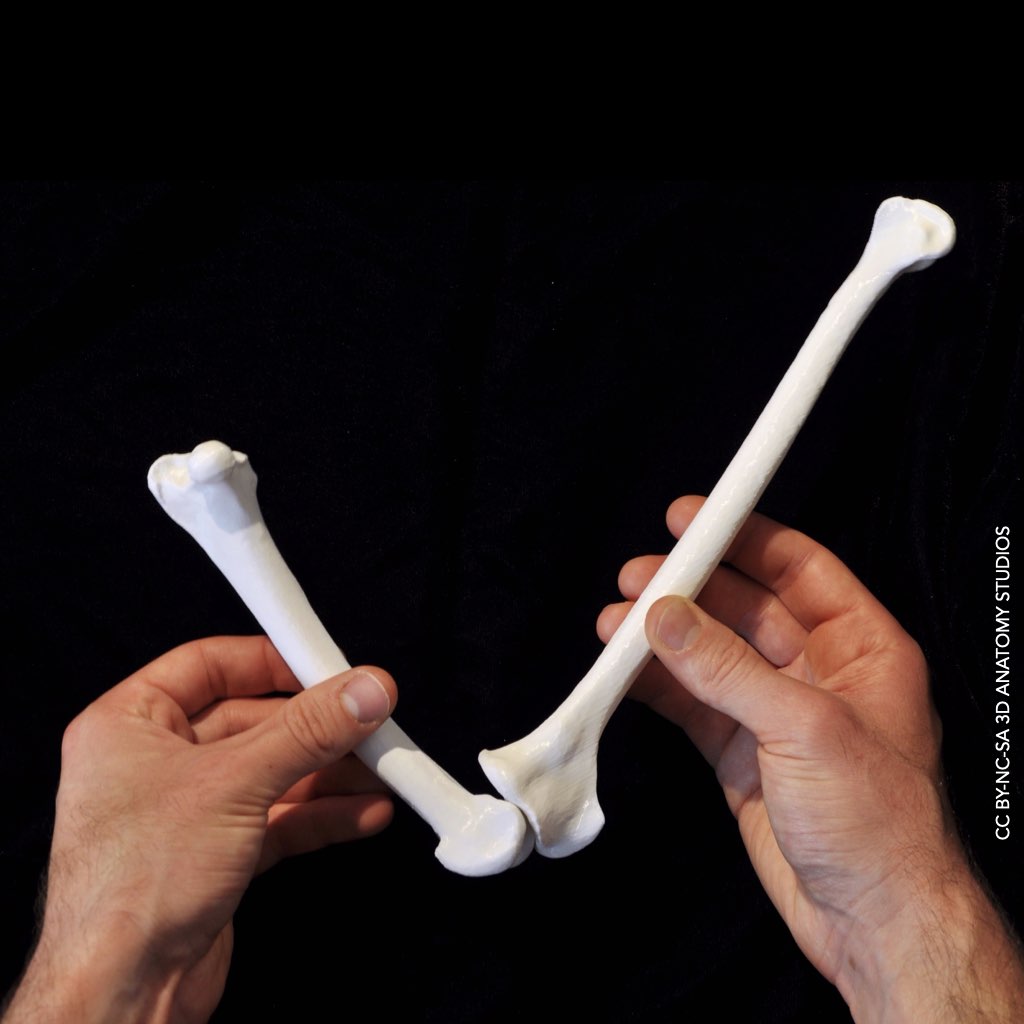
While specimens have traditionally been used to provide this physical modality in anatomy (and there are many benefits of specimen-based learning!), physical models have advantages over specimens, especially when used as a complement to specimens and virtual models. Dissection specimens are typically used just once and then thrown away, whereas models can be used repeatedly. Rare specimens that are damaged through repeated use cannot be easily replaced, whereas models can. Specimens that are too small (e.g., middle ear bones) or too large (e.g., elephant skull) to be handled can be scaled to the appropriate size for handling as a model. And soft tissues, that would otherwise be difficult to preserve for long-term use, can be recreated as a durable model.
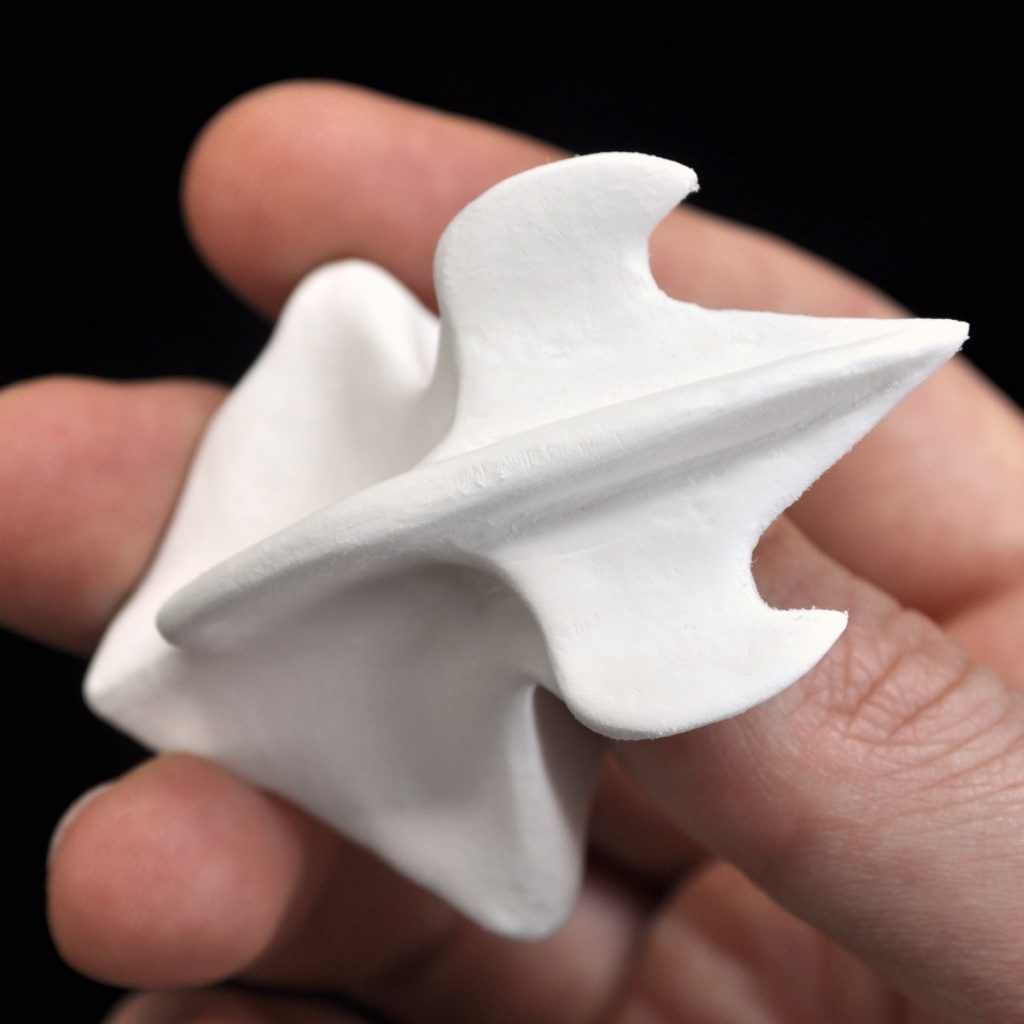
These are all the reasons we love helping people turn their digital data (whether mesh files, medical imaging data, confocal stacks, or photographs) into physical models that will transform their teaching, give them new insights into their research, and add that “Wow!” factor to their science outreach. In this blog post, we walk you through the steps we take in creating physical models so that you know the attention to detail and quality you’ll receive in working with us. Even though we specialize in anatomical models, we’re also happy to work on non-anatomy models too! Once you’re ready to bring your digital data to physical life, contact us to get started!
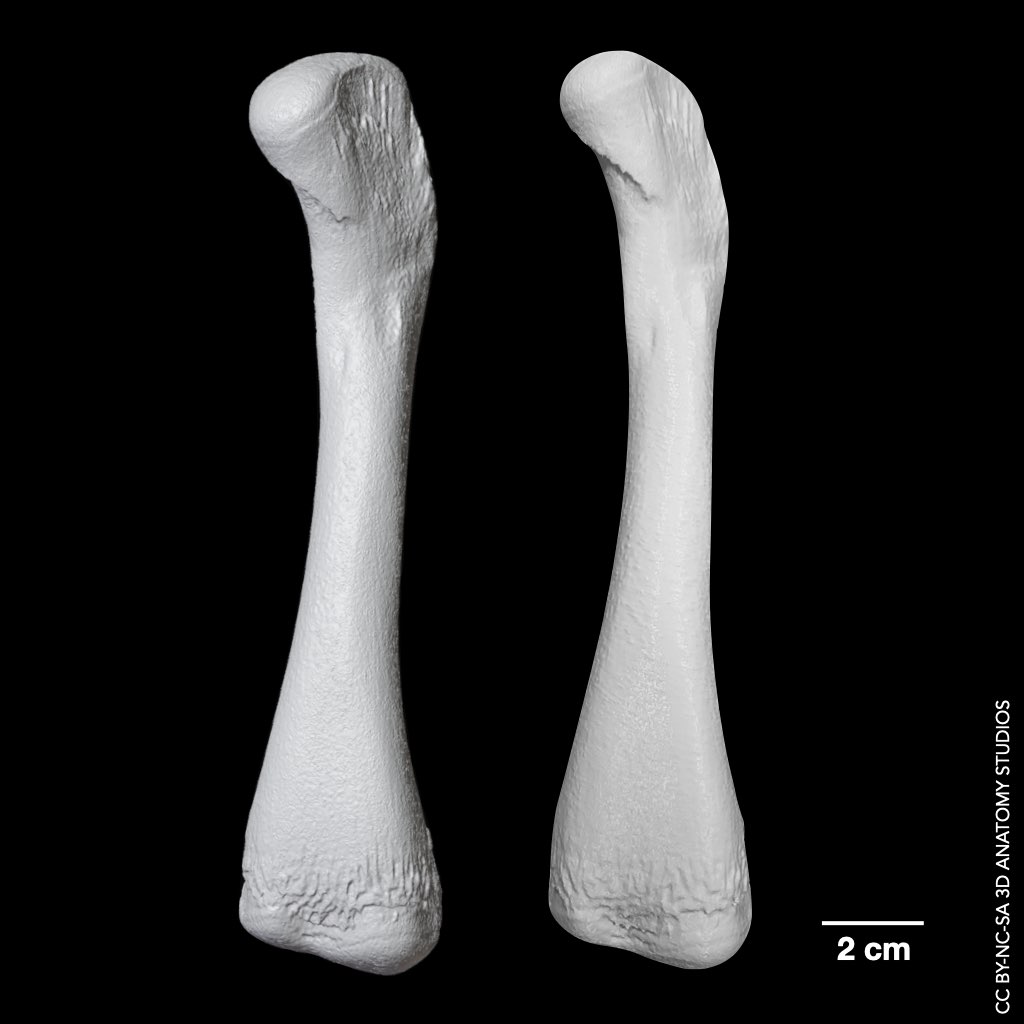
1. Understand your needs
Our first step in creating a physical model is to understand your needs and intended uses for your model. This can begin with you sending us some basic details through our 3D printing service contact form. If all you need is a 3D print of a mesh file (i.e., an OBJ, STL or PLY file with vertices, edges, and faces), we can follow up directly with a quote after we make sure we get the proper scaling.
For more complex projects, it may be necessary for us to follow up with a meeting to hear more about your needs, ask questions, and offer recommendations. For example, if you need to show how multiple structures connect or articulate with one another (e.g., bones of the skull, components of a protein complex), we might recommend 3D prints of each element in a different color with embedded magnets so that the pieces can be easily attached and detached. Or if you need to demonstrate how structures move relative to one another (e.g., a knee joint), we would recommend a multi-body physical model with 3D printed rigid elements joined together with artificial ligaments (e.g., woven polyester) or molded silicone pieces. As expert biologists and anatomists, we “speak anatomy”; this greatly facilitates communication about how to approach particular anatomical features, such as bilateral asymmetry, distinctions between tissue types, etc.
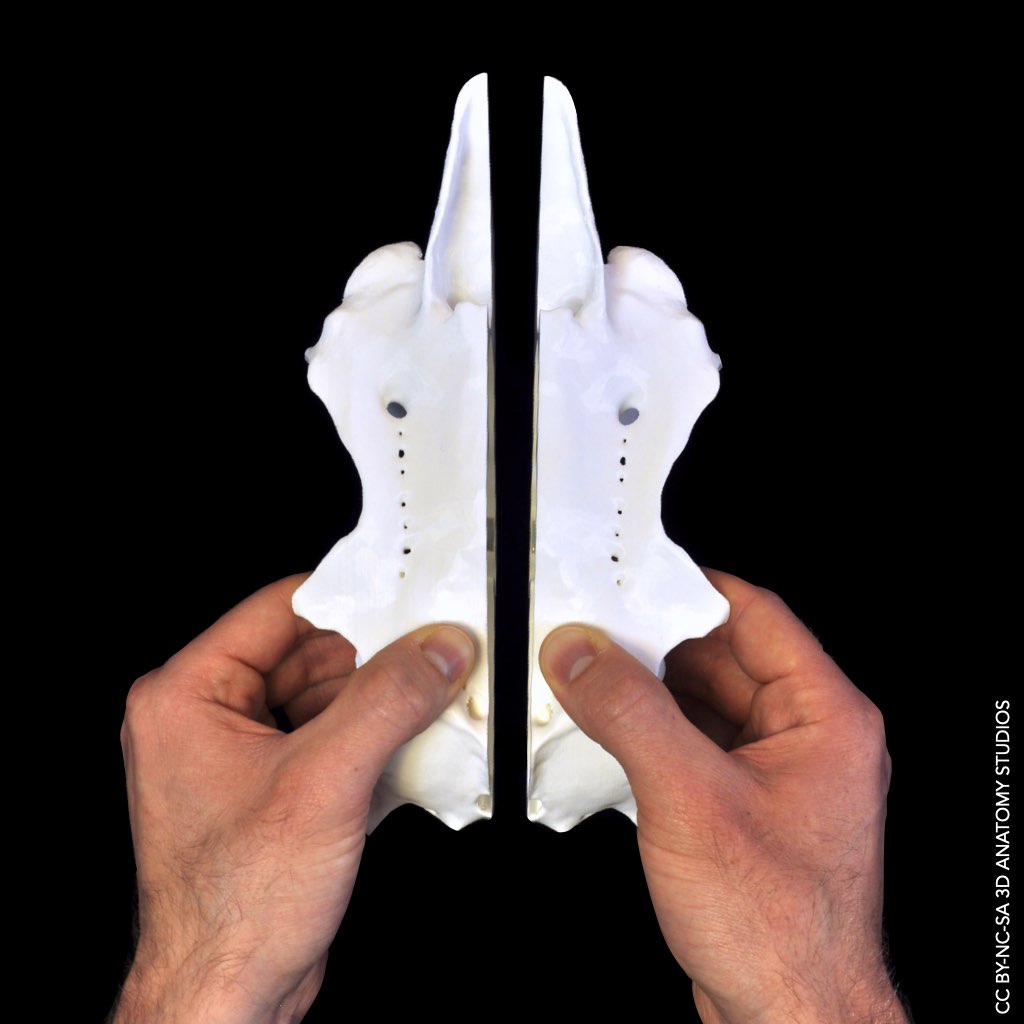
Starting with an in-depth understanding of what you need and how the model will be used ensures that we create a model uniquely tailored to you.
2. Create a quote
Once we understand the full scope of the project, we generate a quote with all the details of the order (e.g., number of prints, number of copies, color, scaling, materials, delivery date, cost) and send this to you for your review. Through the quote, you can make sure we’ve understood exactly what you want and get a clear commitment on cost and delivery. Once we receive payment or a purchase order for the quote, we begin creating the model!
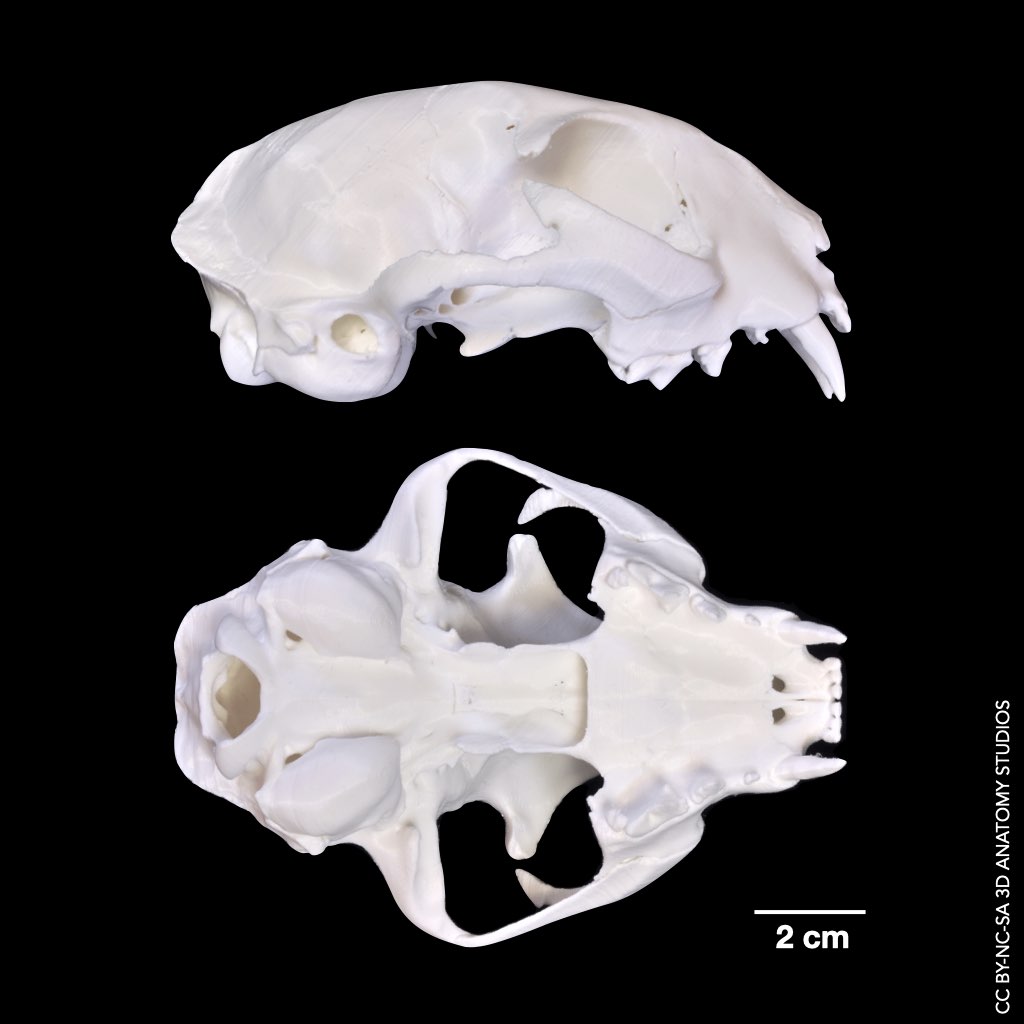
3. Prepare a digital version of the model
The first step to creating the model is preparing a digital version of the model for 3D printing or molding. If you already have mesh data, such as an OBJ or STL file, that you want printed, we can skip this step.
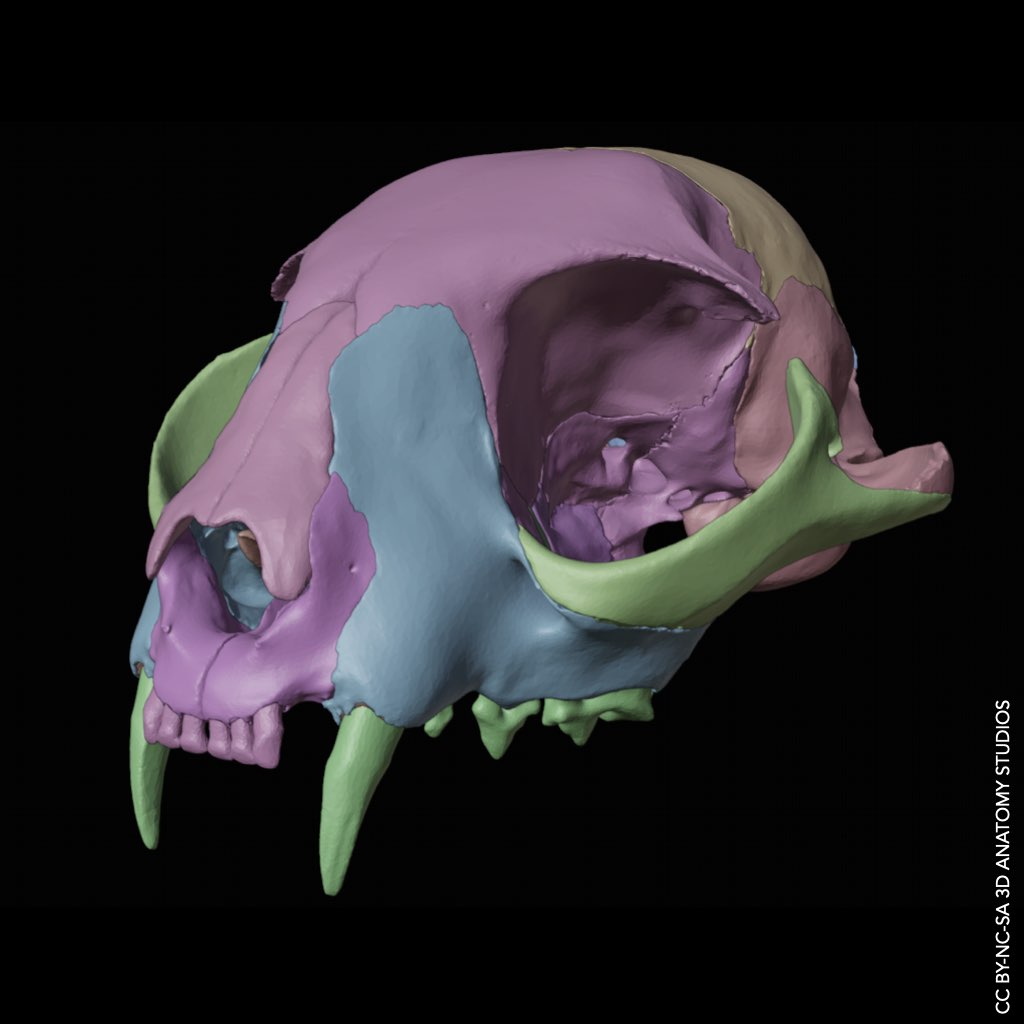
However, in another case you may have 3D imaging data (a CT scan, an MRI scan, confocal microscopy data), from which you would like to create a 3D model. As anatomists with expertise in medical imaging, we can identify and separate the target structures from these data (called “segmentation”) and export the structures as meshes.
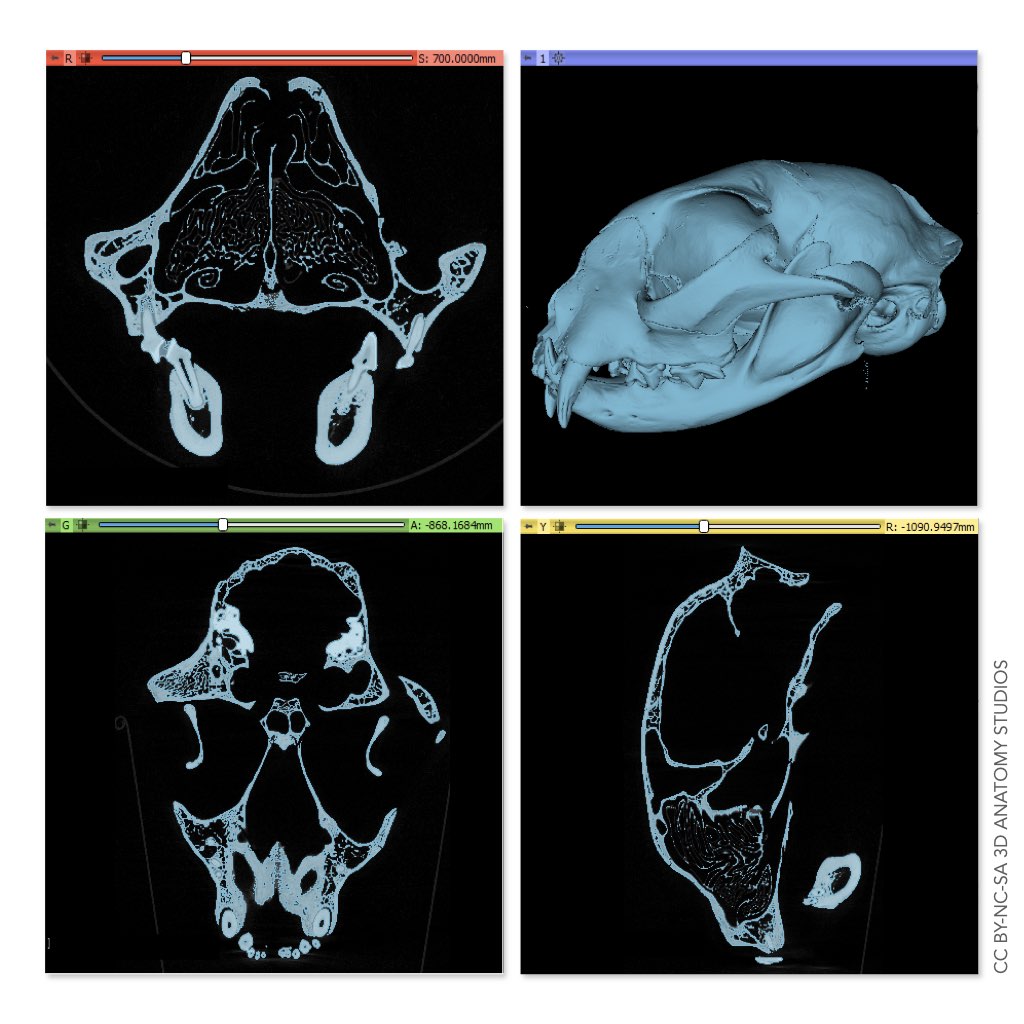
Creating a 3D model doesn’t always require the original data to be three-dimensional. If you don’t have mesh files or 3D imaging data, we can sometimes create 3D models from a series of photographs or even illustrations. If you don’t need a model that matches a particular specimen precisely, a 3D model created from several photographs (e.g., taken from all axial views) is usually within the structure’s natural range of variation. This can be perfect for models that are intended to be conceptual rather than represent a particular specimen.
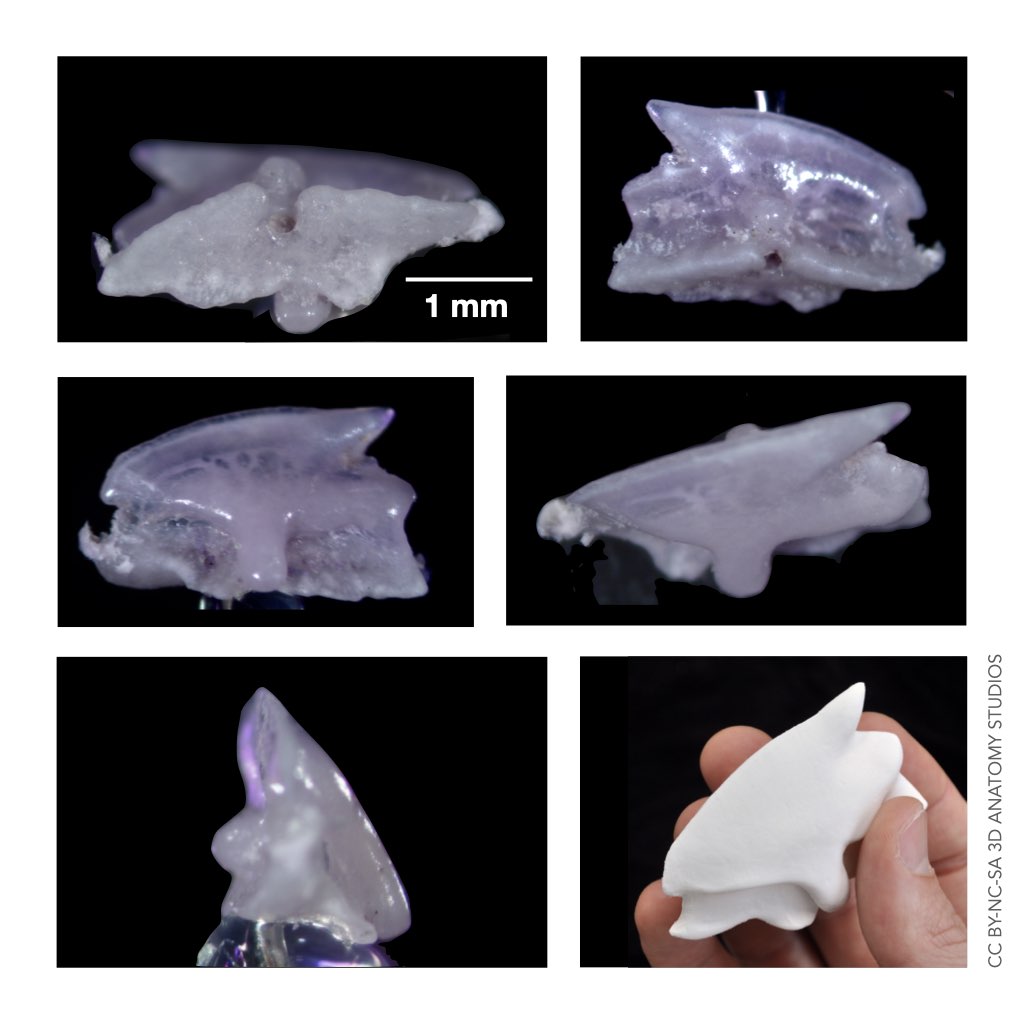
The final step of creating a digital version of the model is removing any artifacts, if requested. For example, the surface of meshes created from medical imaging may have an artificially roughened or bumpy surface as a result of the scanning or segmentation process. Another example is the deformation of a specimen as a result of preservation and storage (e.g., fish fins and bodies bent from being fixed and stored in jars). If you wish, we can digitally correct these artifacts so that the physical model better reflects the natural anatomy, not the scanning or preservation method.
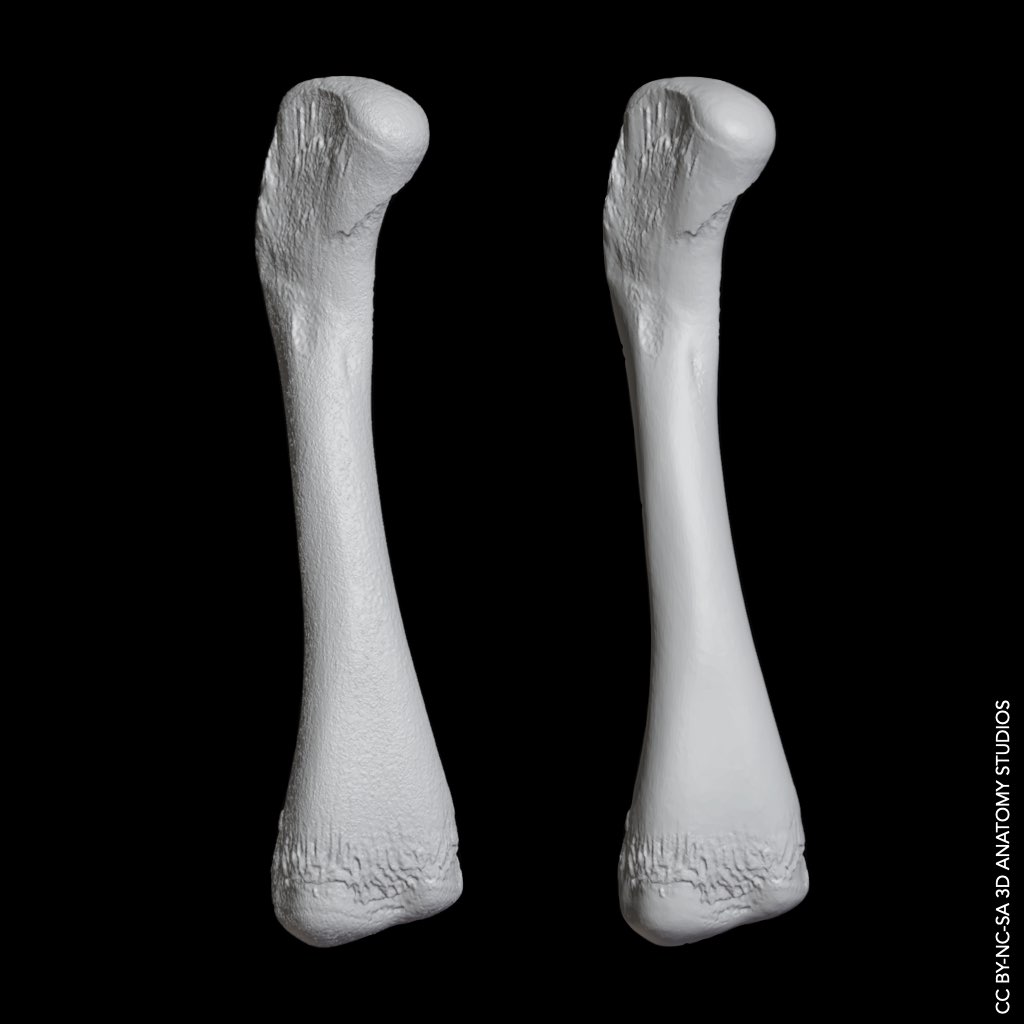
4. Modify the digital model for 3D printing or molding
Once we’ve prepared and cleaned up a digital version of the model, we may need to make modifications to allow it to be 3D printed properly. For example, if the model is too large to be printed or molded as a single unit, we can break up the model into several smaller pieces. Printing long, thin structures attached to larger objects can also be problematic because the thin portions are easily broken when removing the support structures from the completed 3D print. In this case, we can digitally separate the delicate portions of a model, print them separately, and attach them after removing the support structures.
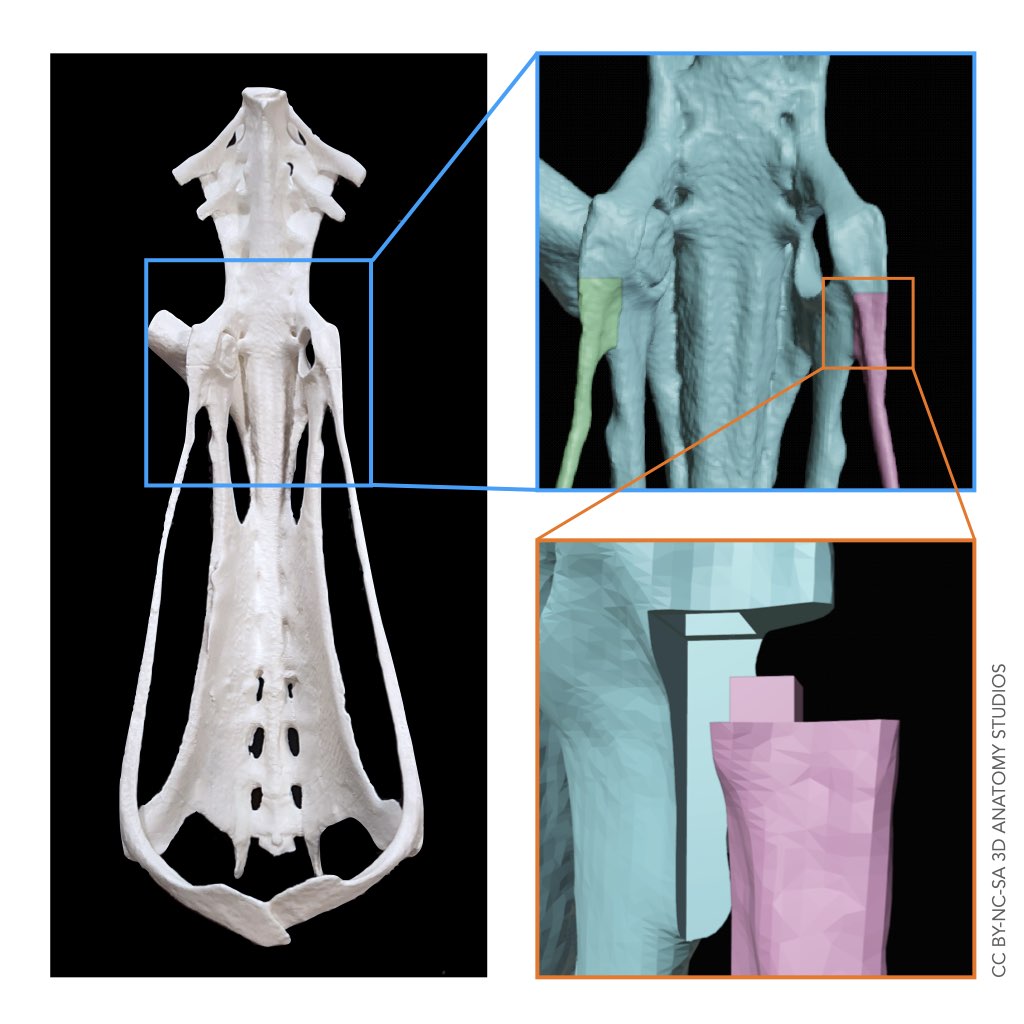
A common problem when 3D printing meshes created from medical imaging data is that if the wall of a structure is too thin, the wall will either have holes or disappear entirely when 3D printed. This is because when the mesh is converted into a file for 3D printing (a process called “slicing”), any portions of walls with a thickness less than a particular threshold are treated as if there were no wall. By inspecting the “sliced” model, we can identify any problem areas and digitally increase the thickness of those areas so that they are printed at the thinnest width allowed by the 3D printer (approximately 1 mm).
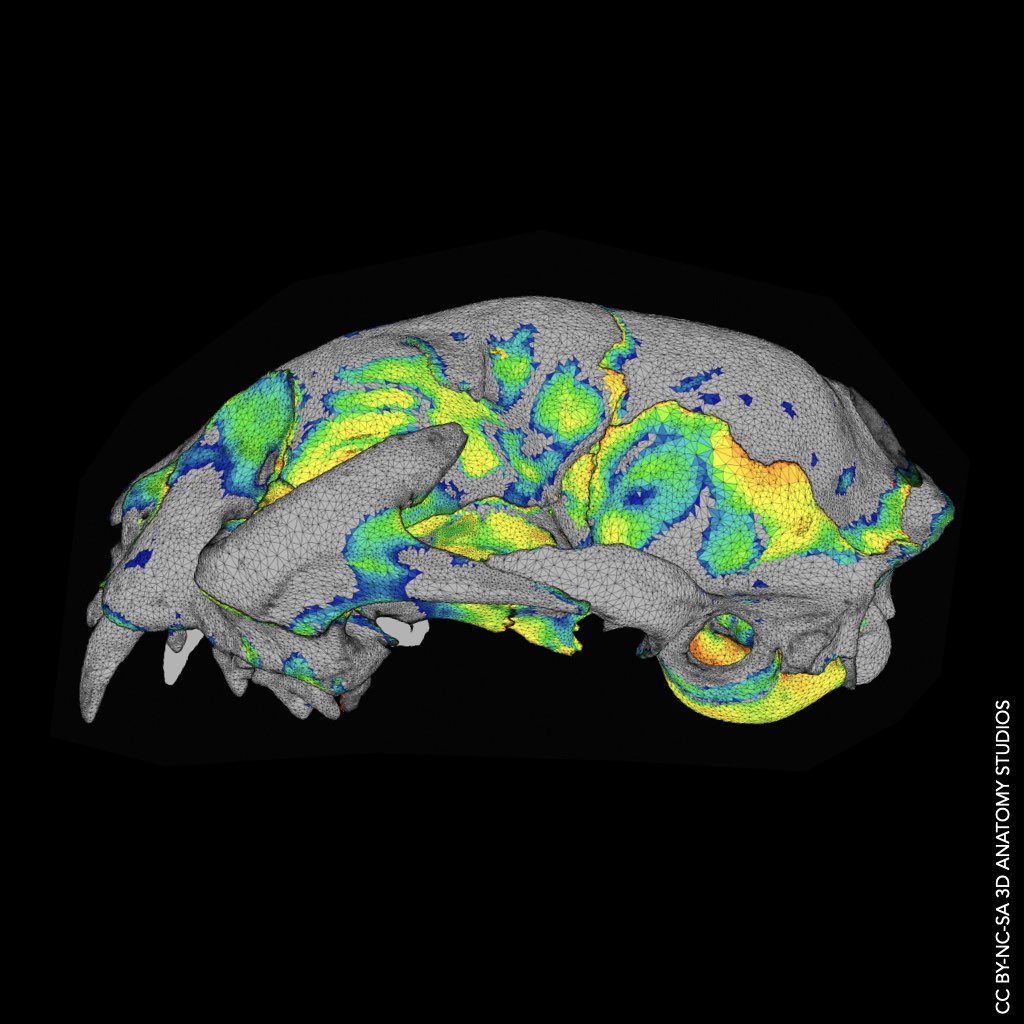
5. Modify the digital model for additional materials
The next step is modifying the digital model to include any additional materials you want in the physical model. For example, if we’re adding magnets to the model, we add holes in the digital model so that after it’s printed we have perfectly sized holes for inserting the magnets.
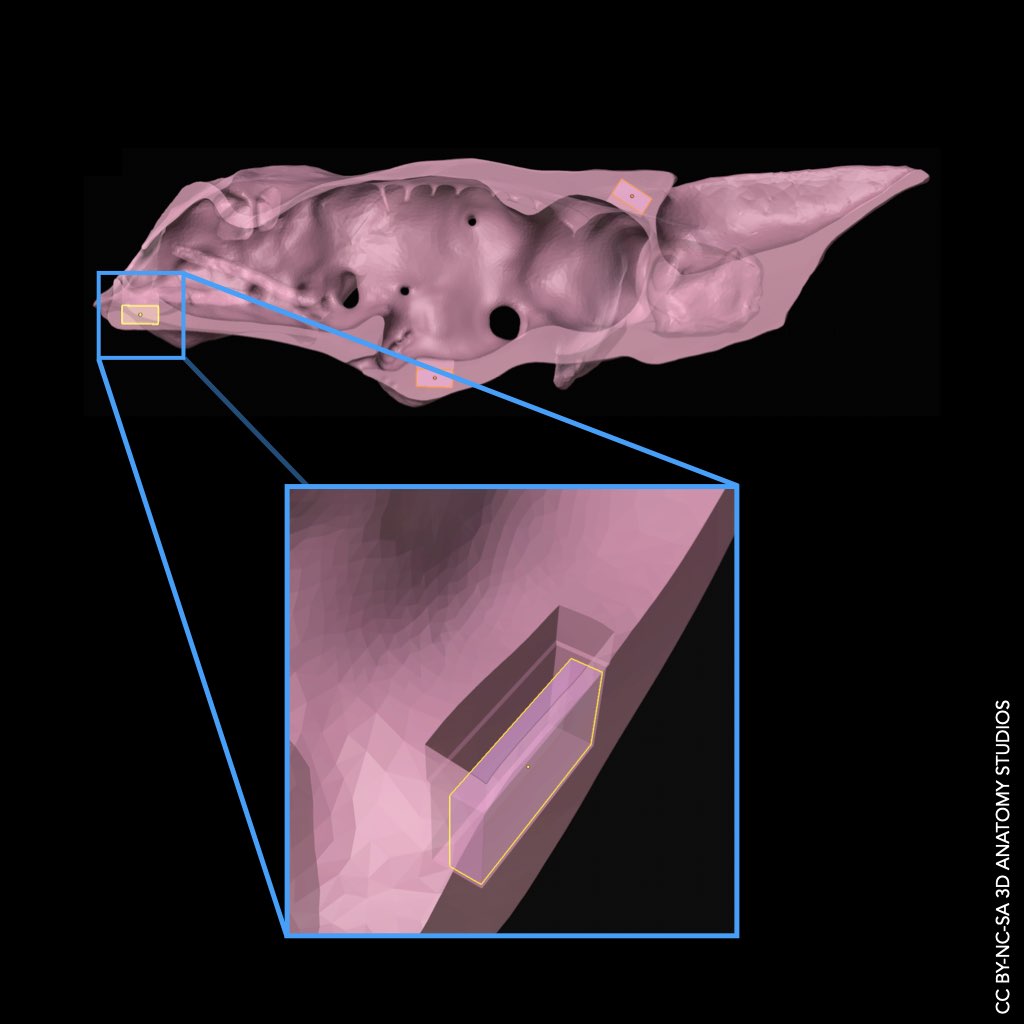
This allows for pieces of the model to be easily attached and detached so that you can easily show the inside and outside of a model or how elements articulate with one another.
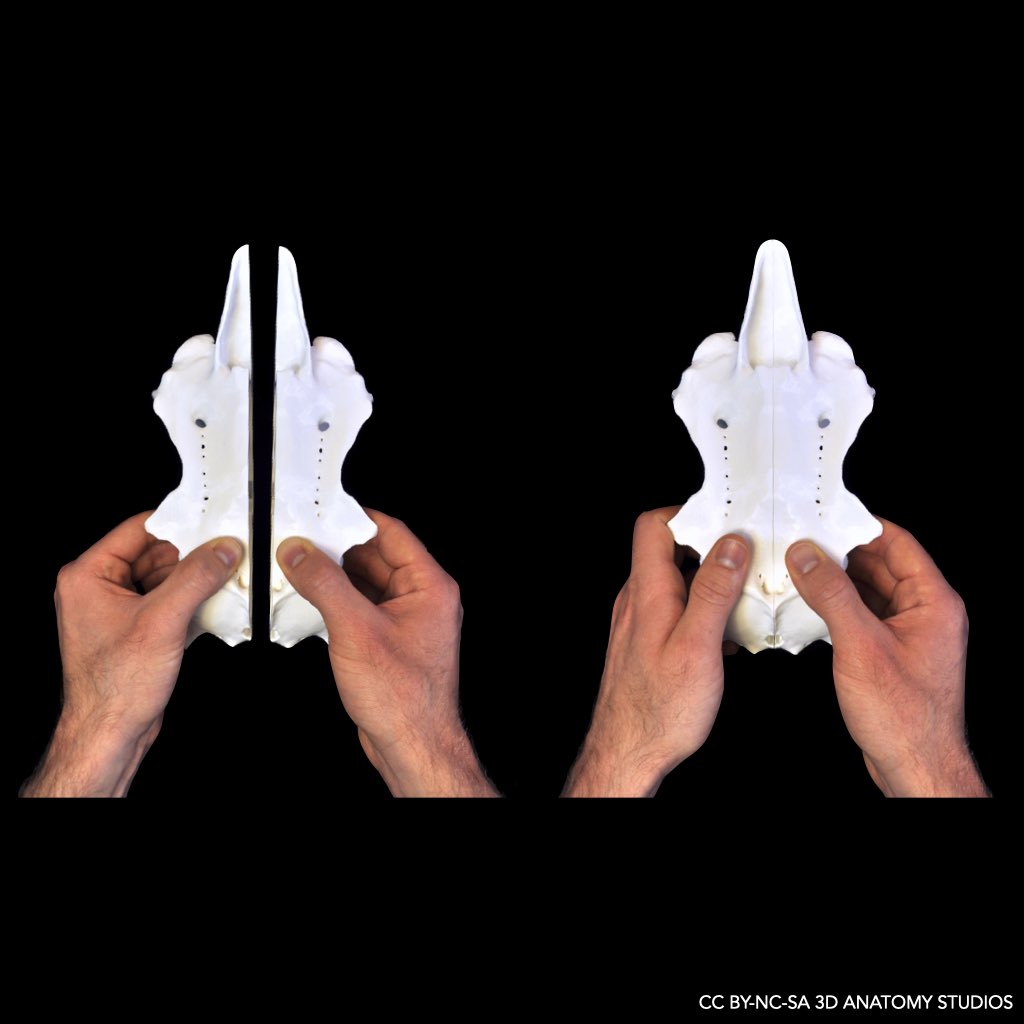
We can also add other shapes to the digital model, such as hooks or pegs, for attaching other materials such as artificial ligaments or molded silicone components.
6. Slice the model
Now that the digital model is ready to be 3D printed, we convert it into a format the 3D printer can “understand” through a process called “slicing.” Since 3D printing builds a 3D object by laying down one layer at a time, this process “slices” a 3D shape into each of these sequential layers. Since a 3D printer must also always print onto something (it can’t print on thin air), slicing also adds support structures so that every part of the 3D printed structure has something underneath it.
One of the goals in slicing a model is to minimize the number of supports needed; the more supports that are needed, the more time it takes to remove and clean the finished print. Another consideration is making sure the supports are attached to the most robust parts of the model; this reduces the chance that the model will be damaged when removing the supports. We test various orientations of the model to find an optimal orientation.
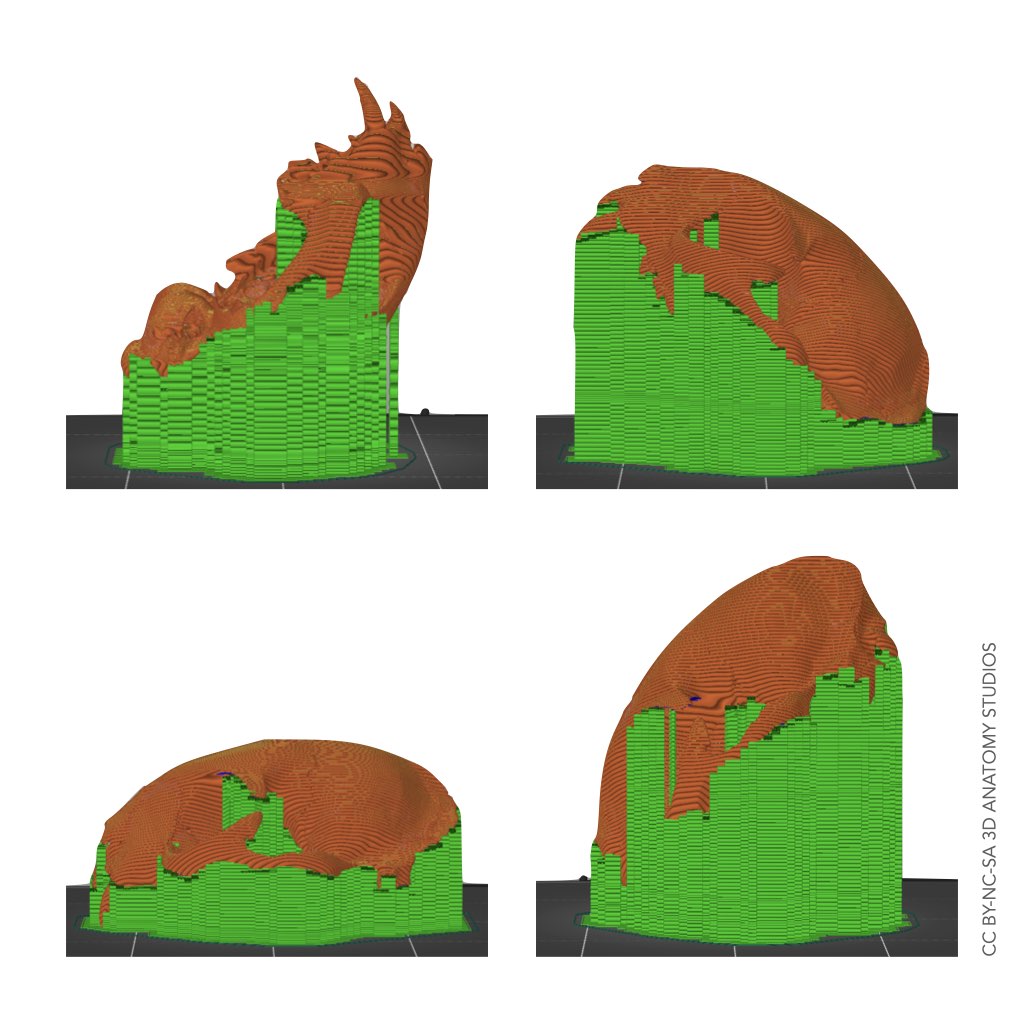
As mentioned previously, a 3D printer works by depositing hundreds, or even thousands, of individual layers on top of each other. The height of those layers determines the resolution of the model in the vertical dimension: the shorter the layer height, the higher the resolution. However, shorter layer heights also increase the total time required for printing because of the greater number of layers.
After we’ve determined the optimal orientation for the print, we set the layer height depending on the resolution that you want. If you don’t need the highest resolution, we can decrease the cost of the print by using wider and fewer layers. The slicing software allows us to even set different layer heights for different regions of the print. We love this feature because it allows us to increase the resolution in flat regions (where layer lines are more obvious) and decrease the resolution in vertical regions to lower the overall print time and cost of your model.
7. Print the model
At this point, we’re ready to 3D print the model! It can take 15 minutes or more than a day to 3D print a model, depending on the size and resolution. While our printers don’t require constant monitoring (can you imagine?!), we do check on them throughout the printing process to ensure everything is printing properly and replace the filament if the printer runs out mid-print. For projects where pieces must snap or fit together, we may print a series of prototypes to test which dimensions give the intended functionality.
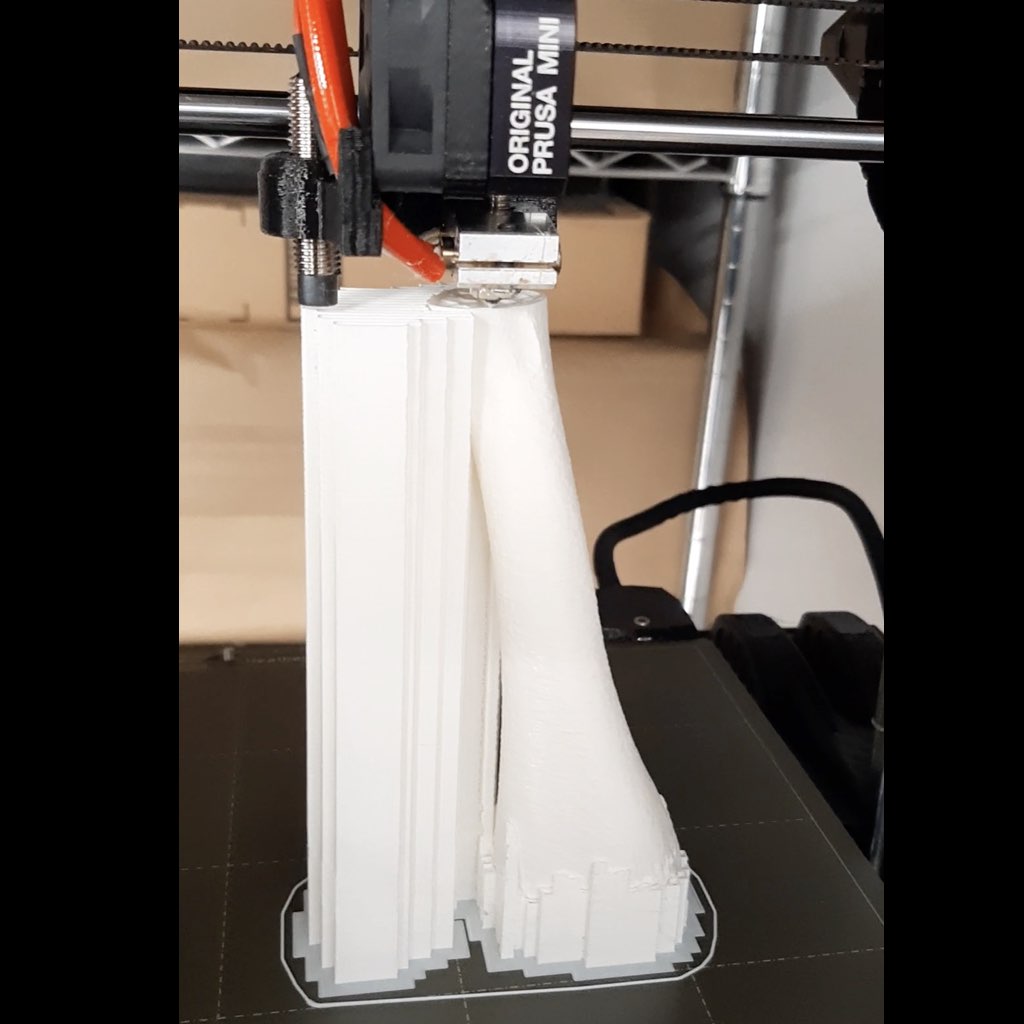
8. Clean and post-process the 3D prints
As mentioned previously, any overhanging structures on a model require “supports.” So once a part has finished printing, we remove any of those support structures. This must be done manually but we’ve developed techniques and tools to do this quickly. The time to remove the supports depends on the size and geometry of the model and can take anywhere from a few seconds to up to 15 minutes.
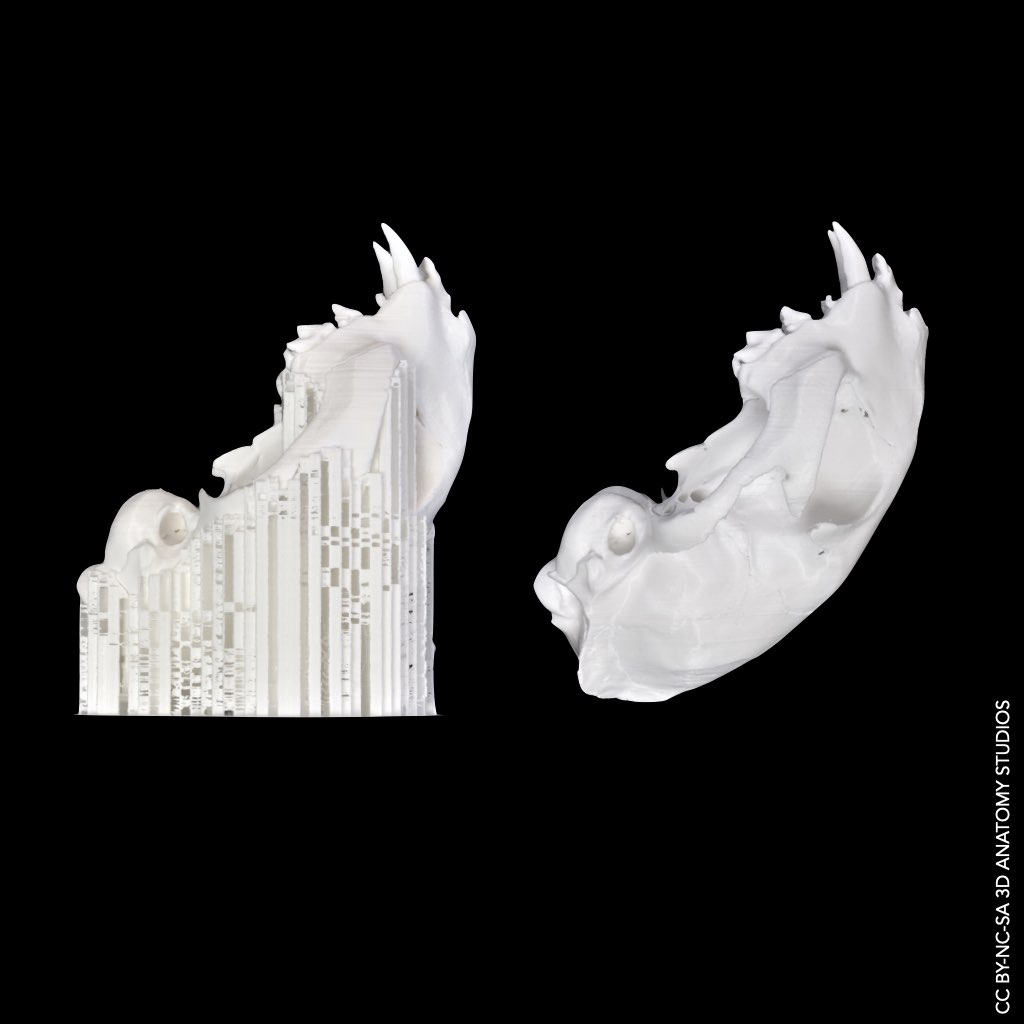
Sometimes, the printing process leaves thin strands of plastic on the printed part, called “stringing”; this is a natural part of the printing process when using plastic filament. We use a heat gun to quickly blast away these thin strands.
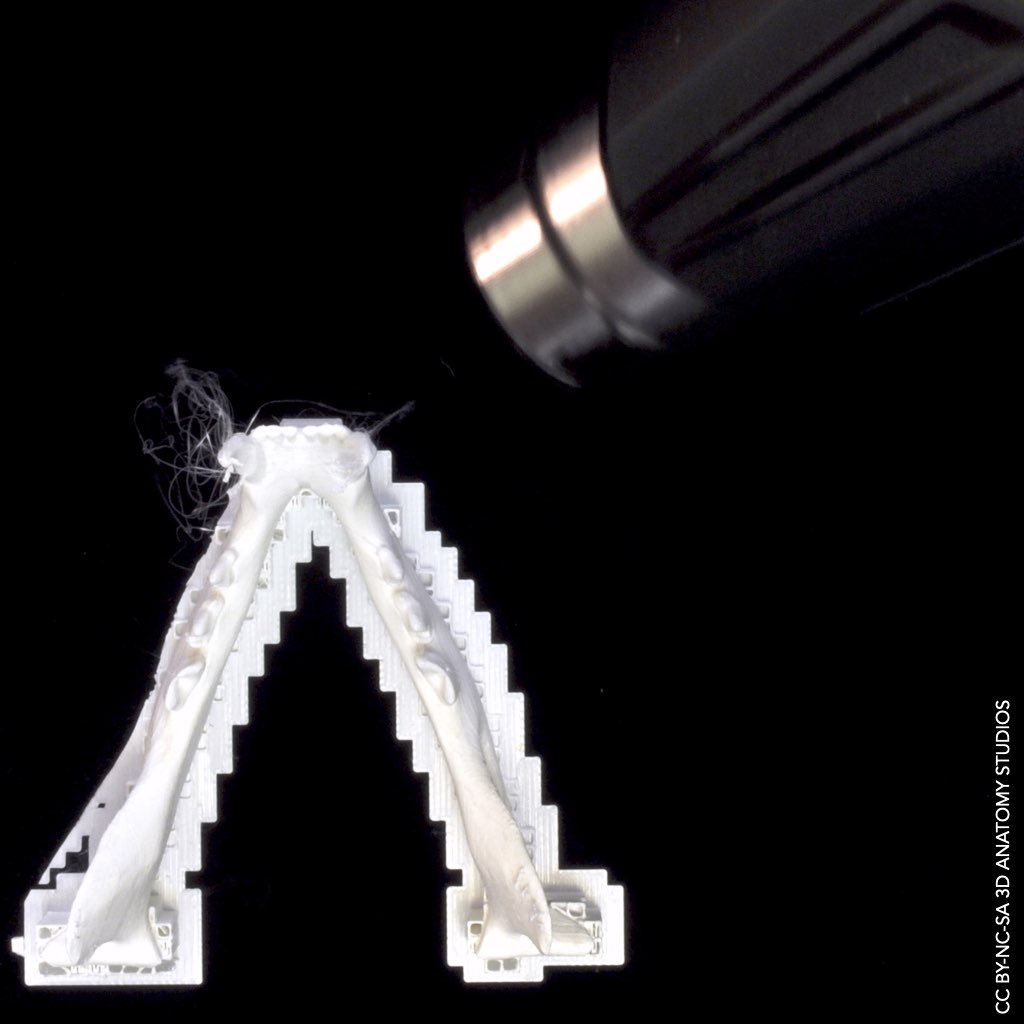
The printing process can also leave surface artifacts, such as poorly adhered layers and uneven areas where support structures were attached. If present, we remove these artifacts as best as possible using a grinding tool.
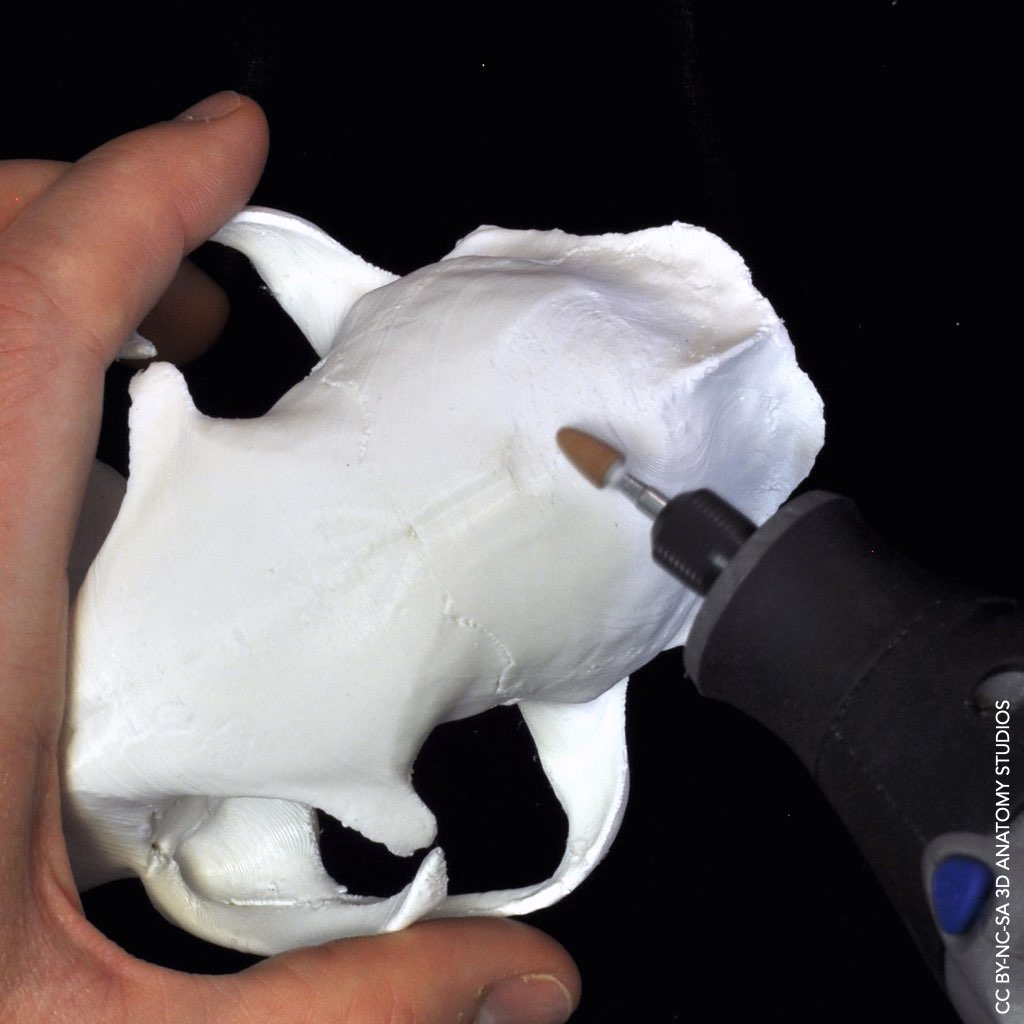
3D prints created using the filament extrusion process have visible layer lines, although these are generally less than 0.20 mm thick. If you would rather have a finished surface, where the layer lines are not visible, we can sometimes offer this, depending on the size and complexity of the model. To remove the layer lines, we manually grind and sand the surface, giving it the feel of terracotta or unglazed clay.
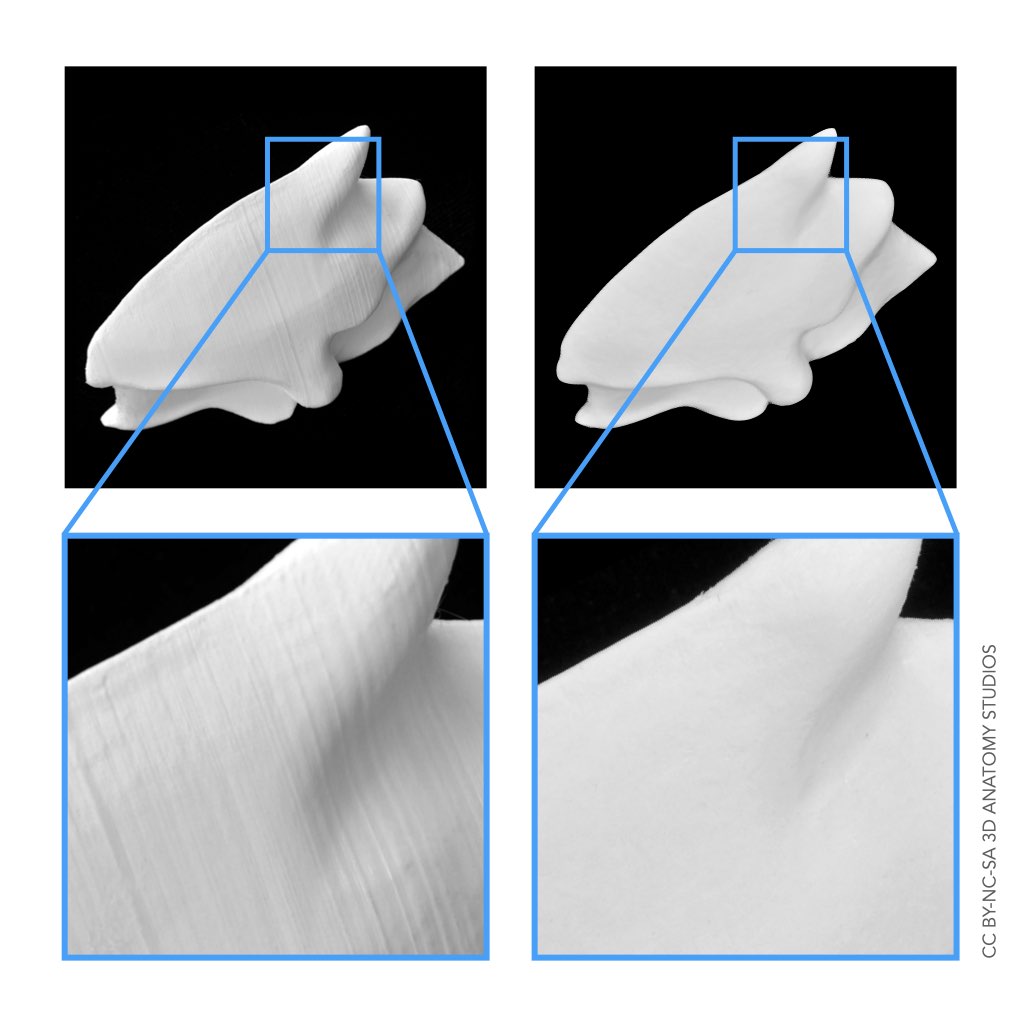
9. Combine parts and add additional materials
For the final step of creating a model, we glue together any parts that we printed separately. We also add any additional materials to the 3D printed parts, such as artificial ligaments, silicone-molded components, or magnets. If we’re adding magnets, we insert these into the compartments that we added to the digital model (ensuring the proper orientation!) and fill and cap the compartment with clear melted plastic so that the magnet doesn’t come out.
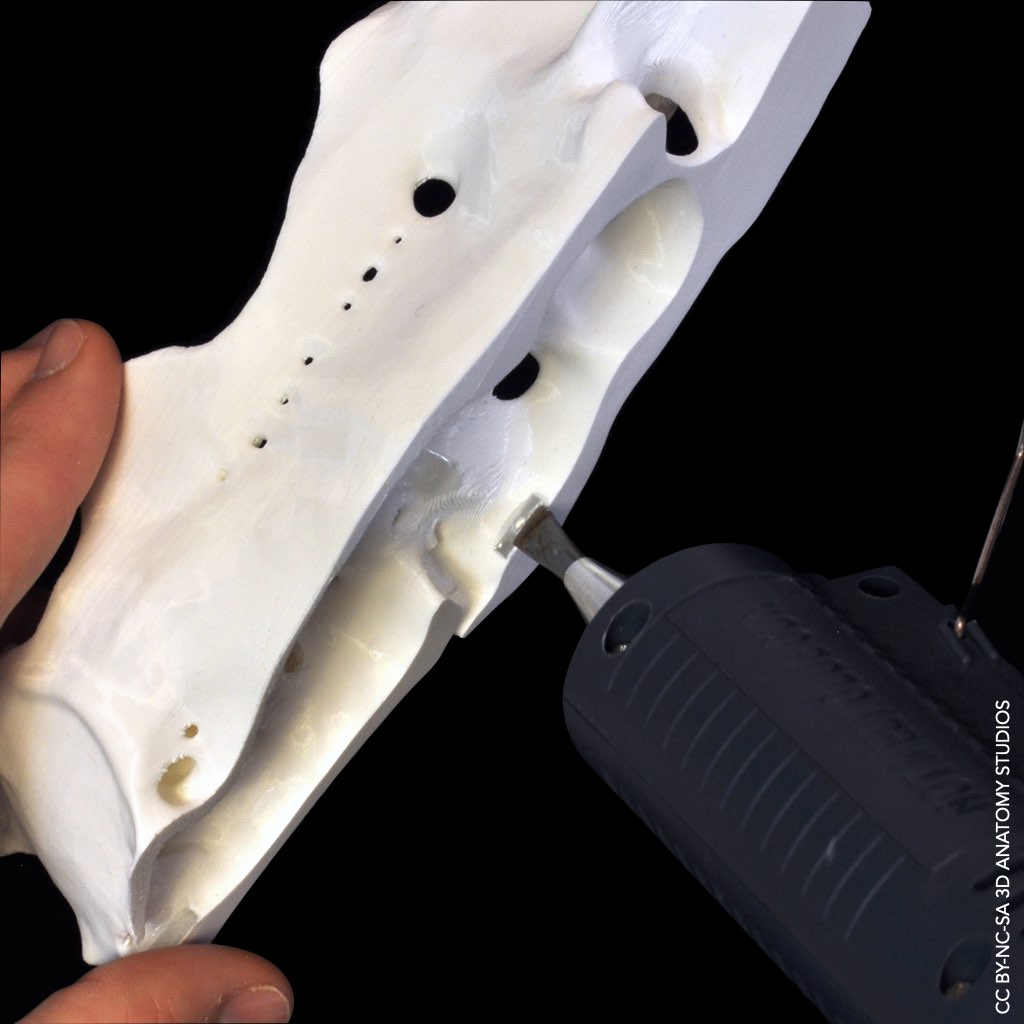
10. Pack and ship the model
Once we’ve completed your model, we carefully pack it up (using 100% renewable and recyclable materials) and ship it to you!
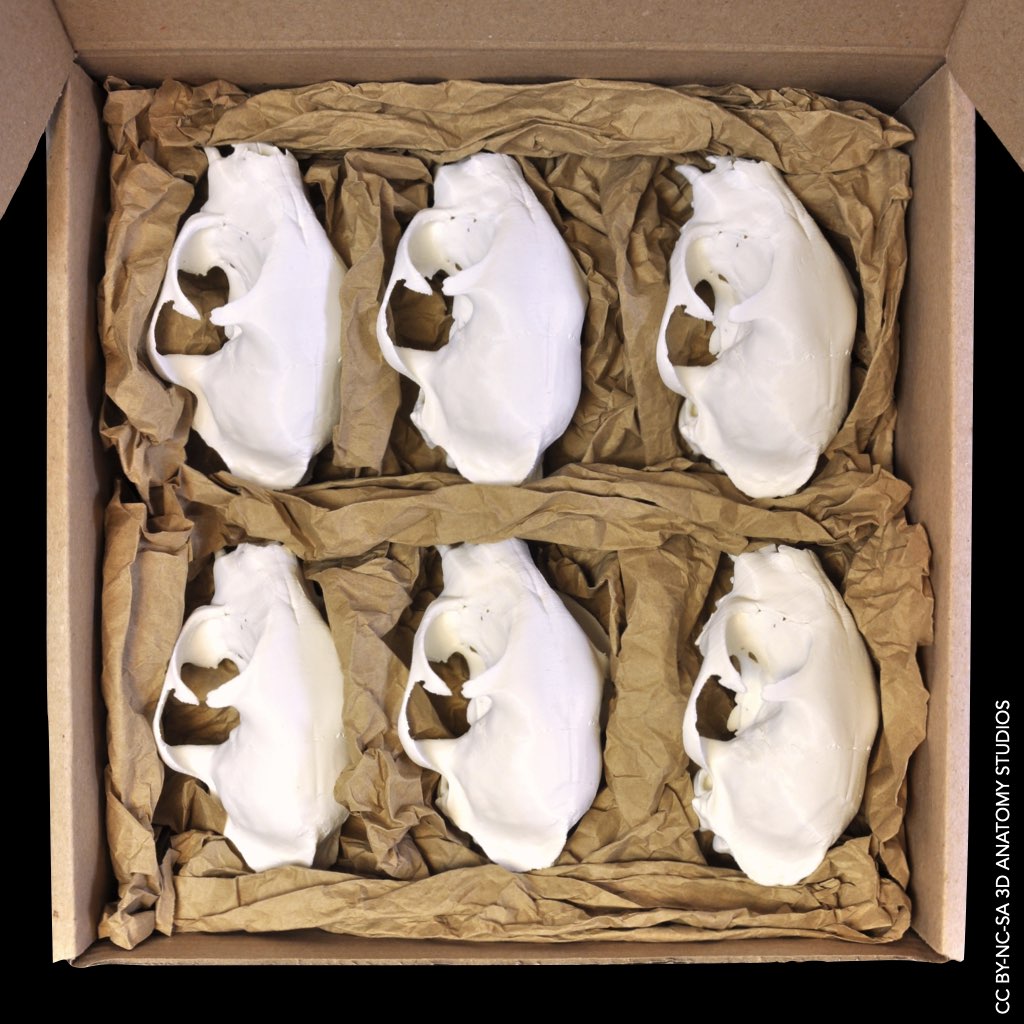
We hope that this post has sparked some ideas on how you can incorporate physical models into your work, research, or teaching. We also hope it has given you an idea of the care and expertise you will receive in working with us. Are you ready to wow your students, impress your colleagues, and gain a new perspective through hands-on, multisensory interaction? If so, start by contacting us. We look forward to hearing from you!
Have a question or comment? Please leave it below!
Written by Aaron Olsen
Edited by Naomi Robson
Images and photographs by Aaron Olsen